3-Step Guide to Effective Expansion Joint Planning
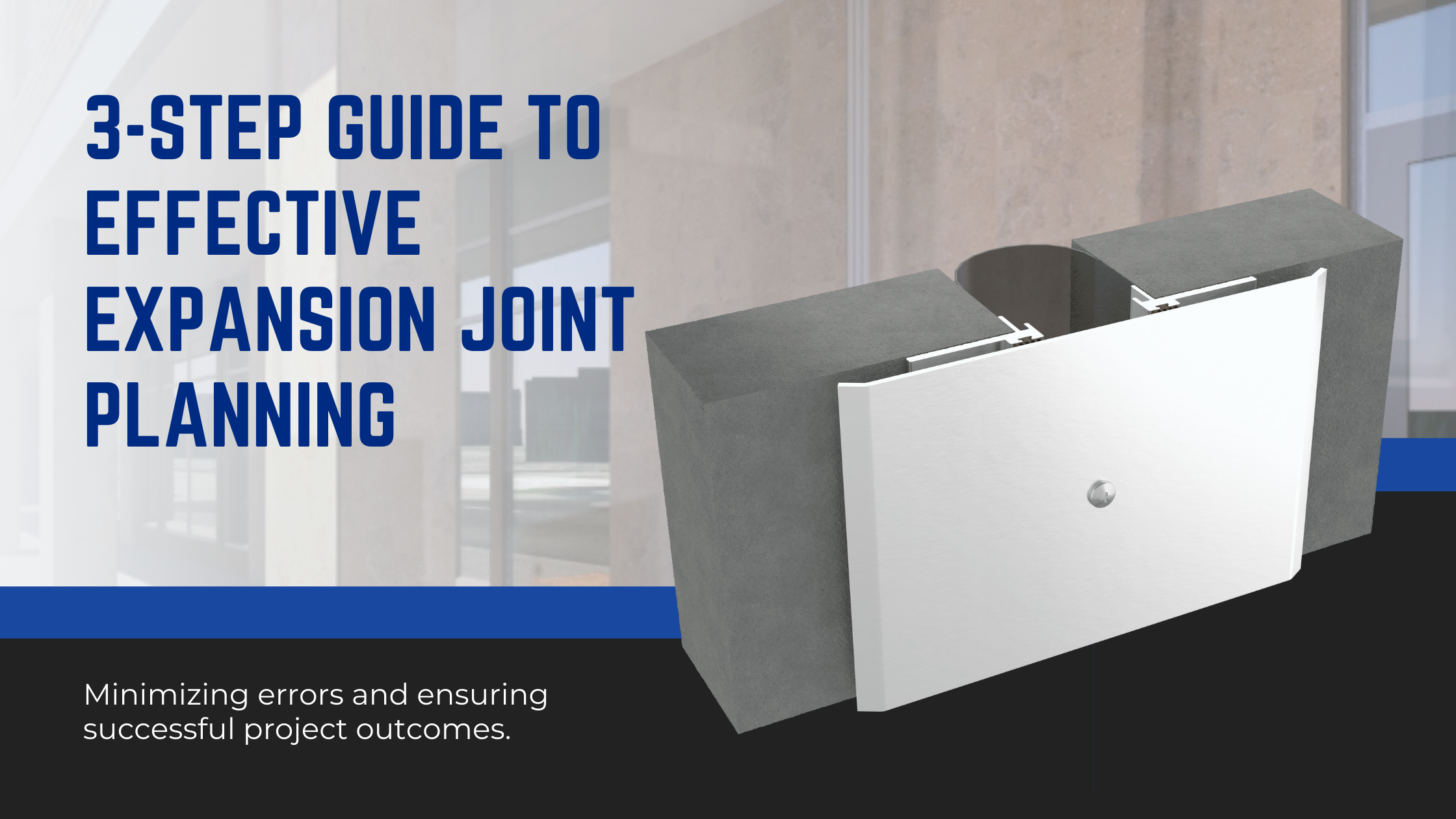
As manufacturers of Expansion Joint Systems, we frequently encounter common mistakes that lead to bidding confusion and ultimately, costly change orders in construction projects. In this article, we will shed light on some of the prevalent issues found in construction documents, along with a three-step design process to minimize errors and ensure successful project outcomes.
Common Mistakes in Expansion Joint Applications:
Mismatched Joints:
One common issue arises from selecting the wrong joint for the application location. This can lead to complications in construction and often results in change orders. Different areas of a building may require varying degrees of flexibility and movement accommodation. For instance, a joint designed for heavy traffic areas may not be suitable for an exterior wall where movement is less frequent. Mismatched joints can result in performance issues, compromised durability, and the need for costly replacements or modifications.
Inadequate Ratings:
Failure to choose expansion joints with appropriate fire, sound, or moisture ratings can jeopardize the safety and functionality of a building. For example, using a non-fire-rated joint in a fire separation area may violate building codes and pose serious risks. It is crucial to thoroughly understand the environmental conditions and regulatory requirements of each application to ensure the selected joints meet the necessary standards.
Mismatched Finish:
The aesthetic aspect of expansion joints is often overlooked. Selecting joints that do not align with the desired finish can impact the overall look of the building. For instance, a mismatch between the joint color and the surrounding materials can be visually disruptive. Careful consideration of the intended finish, whether it be carpet, tile, or another material, is essential to maintain both functionality and visual harmony.
Lack of Detailing:
Incomplete or inconsistent detailing in construction documents can lead to confusion during the installation phase. Without clear and comprehensive detailing, contractors may misinterpret specifications, resulting in incorrect installations. A lack of attention to detailing can lead to delays, rework, and increased project costs.
Absence of Joint Lists:
A common pitfall is the absence of a comprehensive list of all required expansion joints is a common oversight. Relying on a single model number for one of many joints needed for a project can lead to confusion and errors. Each joint serves a specific purpose, and having a detailed list ensures that the right joints are used in the right locations, preventing unnecessary complications and rework.
Manufacturer Issues:
Specifying a manufacturer that is out of business or doesn't produce the required joint can lead to project delays and additional costs. It's essential to verify the availability and reliability of the chosen manufacturer. If issues arise, a last-minute change in the specified manufacturer may necessitate redesigns and adjustments, impacting the project timeline.
Addressing these common mistakes in expansion joint applications requires thorough planning, attention to detail, and collaboration between designers, engineers, and manufacturers. By understanding the specific needs of each application and selecting the right joints accordingly, construction professionals can ensure the longevity, safety, and aesthetic integrity of the built environment.
The Importance of Early Planning:
To mitigate these issues, a three-step design process is recommended:
-
Plan Joint Placement Early:
Early integration of expansion joints in the design process is crucial. This allows for coordination with complex mechanical, electrical, and plumbing systems, preventing the need to cross expansion joints, which often leads to errors.
-
Develop and Coordinate Design:
Work closely with engineers to determine joint placement, finishes, and ratings. Key considerations include managing movement and building conditions, collaborating with structural engineers, determining joint width and location, assessing aesthetic and performance impacts, and addressing thermal, water, sound, and fire separations.
-
Detailed Scheduling and Specification:
Create a detailed schedule that outlines the location, substrate, finish, type, and corresponding details for each expansion joint. Clearly specify each type of joint to avoid ambiguity during the construction phase.
Schedule Example:
Mark | Location | Substrate / Finish | Type | Detail |
---|---|---|---|---|
A | First Floor | Concrete/Carpet | EM | 1/A1.08 |
B | Exterior Wall | Masonry/Grey | CP | 3/A1.08 |
C | Parking Deck Entry | Concrete/SS | CS | 7/A1.08 |
D | Parking Deck Floor | Concrete/Grey | CP | 5/A1.08 |
E | First Floor at Wall | Concrete/Carpet | CC | 2/A1.08 |
F | Roof | See Roofing Details | RR | 11/A1.08 |
Nystrom understands the codes and complexities dealing with Expansion Joint Systems. To see how Nystrom can help on your next project, please visit www.nystrom.com.
Contact a Rep